FUCK!
I crashed the head or the collet or something on the Rong Fu CNC mill. Details to follow.
~!~!~!~!~!~!~!~!~!~!~!~!~!~!~!~
Ok, well. It isn't the end of the world. Full explanation behind the
cut.
Some guy brought his carb in for the free test. It's a 2-bbl Ford carb (or Motocraft if you prefer that) from the 80s with the full electronics suite: mixture control solenoid, electric choke, and throttle position sensor. On these ones the throttle position sensor is mounted on the side of the base and our regular adapters that we would use to test didn't fit, they needed a notch cut out to accommodate that tps. Mike or somebody made what I believe to be a slightly hokey adapter that goes on top of the standard one. A couple years ago I decided I didn't like that and I grabbed one of the standard 2-bbl Ford adapters and ran over to the mill and cut out a notch for that tps. It came out fine, and it was much nicer than before. And we continued to use that adapter for a couple of years. Until today when this guy brought his carb in, I got ready to throw it on the engine, but his TPS like hangs down lower than normal. I'm guessing it's got to be an aftermarket part, or I can imagine a possibility of his TPS being off of a throttle body for fuel injection, or something like that. We'd used this adapter for hundreds, if not thousands of carbs, but this dude's tps was just different and the carb didn't sit down on the adapter correctly. So today after lunch, not that I had time for this or anything, but this guy was calling up on the phone bitching about how we hadn't tested it yet (just brought it in yesterday), so I ran over to the mill, clamped down the adapter I'd milled out before, and fired up the computer. I coulda done it by hand, but it comes out so much nicer by computer. I didn't bother writing a program for it or anything. It's honestly been a year or maybe even two since I use the CAM program, so I did what I often do when I just want to spit out something simple, I use the jog function.
So I'm cutting away, happy as can be. The way it's always been set up is the computer is behind the mill, and facing away from it. Donno why, it's actually not very user friendly or anything that way. Anyway, I was attempting to type in a command for 0.040" down. It started moving down at 6 ipm, and the spindle's spinning away, and it keeps going down, down, down... "FUCK! STOP! THAT'S MORE THAN 40 THOUSANDTHS! NO NO NO! Z UP! Z UP!" What I actually punched in was to go down 400 thousandths: almost half an inch. It kept moving down, and I started mashing the "jog up" button for the Z axis, but it wouldn't do that command until it finished with the down command. The collet hit a stud sticking up on the adapter and ground down and sprayed out sparks until it actually wore down the spindle motor and it stopped, at which point I was already franticly reaching for the power switch to the spindle motor. The spindle shut off, and the computer then carried out my z-up command. But not before grinding up the stud and chudding the collet.
Pics!@
The stud.
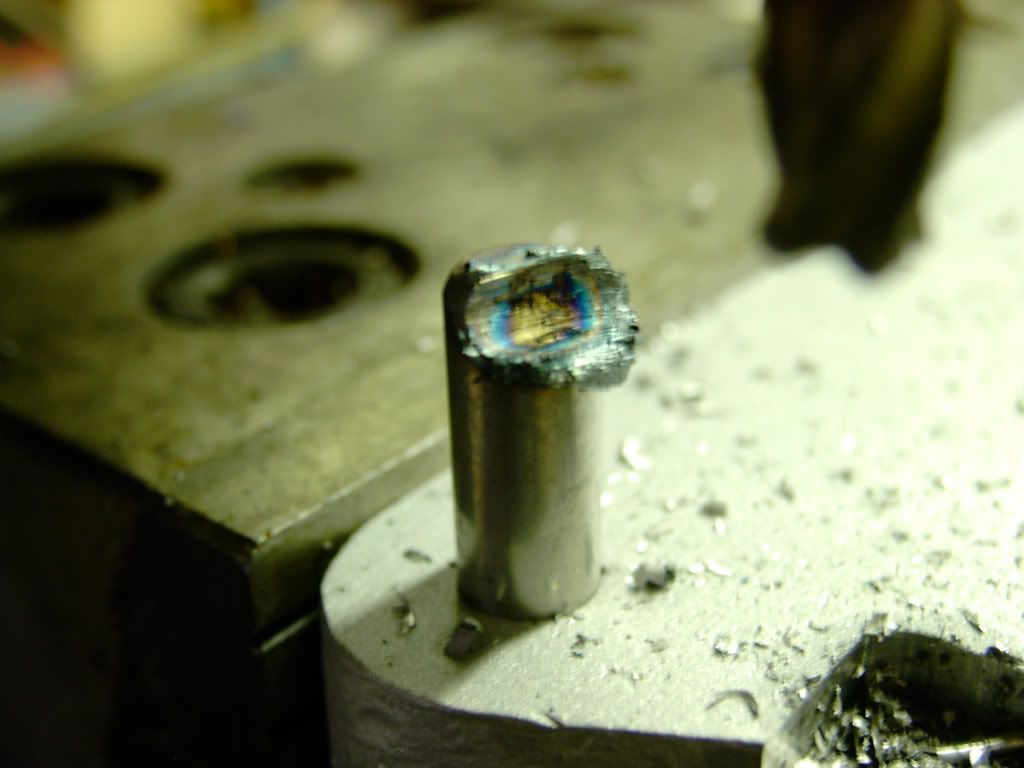
Where it's buggered up: that'd technically be the head I think, eh?
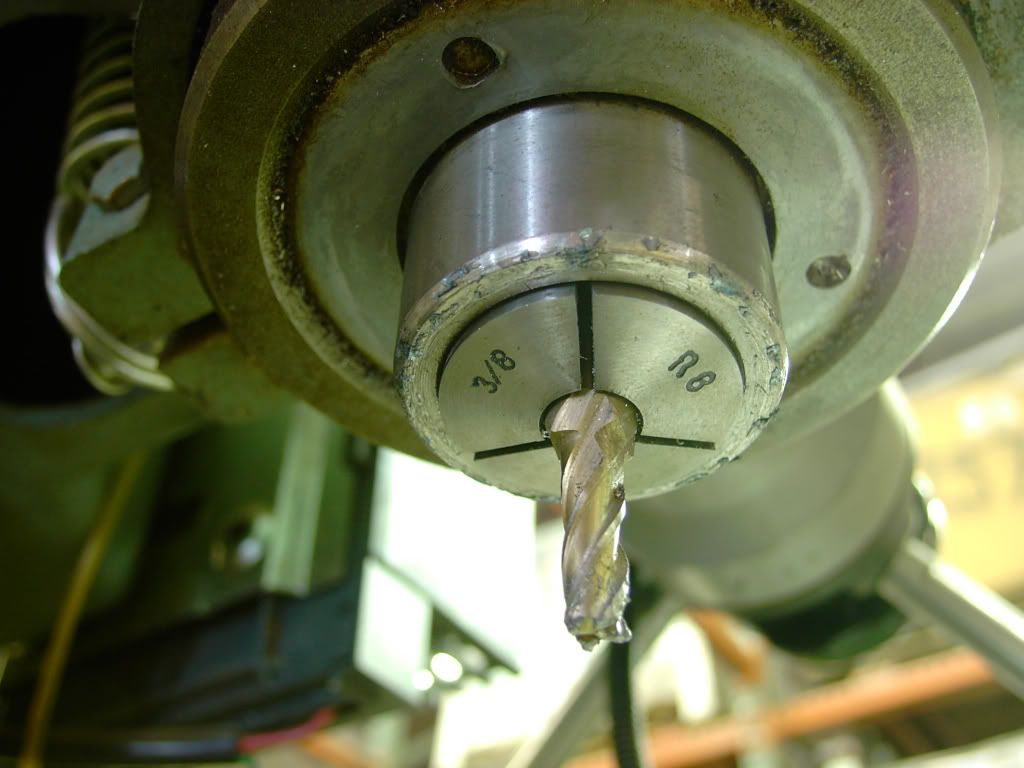
I don't think all that damage is me, actually.
After I discovered it wasn't quite so bad as I thought I continued on with it. More pics of that:
Eh, after reviewing the rest of the photos it looks like they all pretty much suck. Bad lighting or blurry or something. I do have a couple decent shots of the finished product tho:
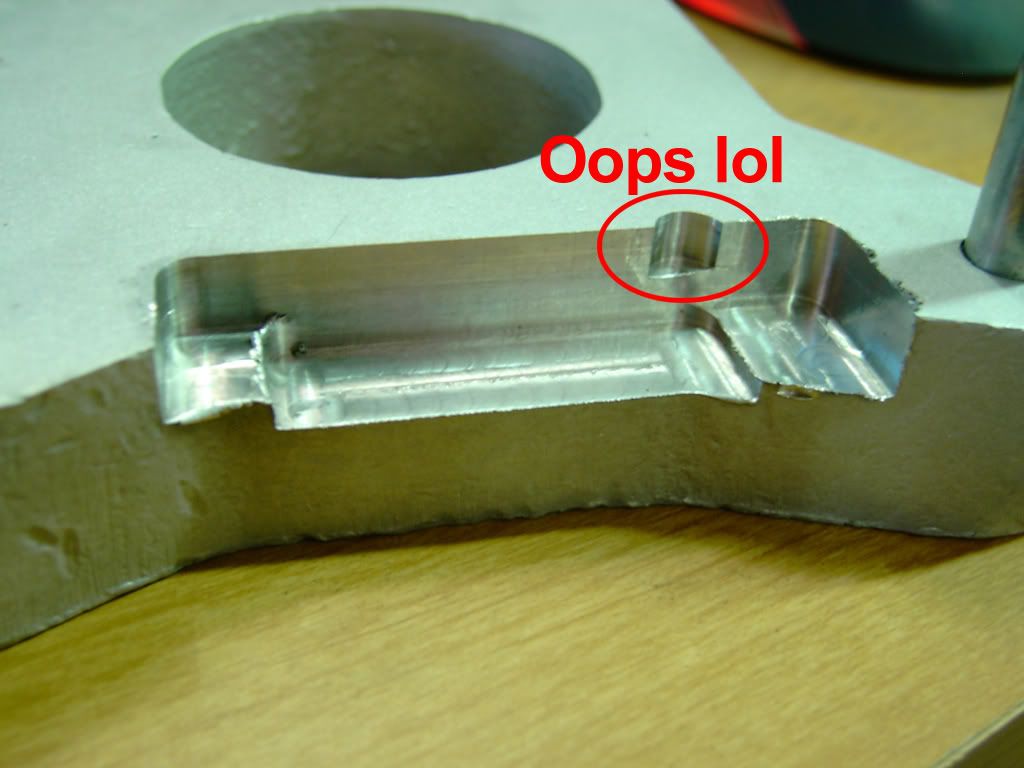
You can clearly see, even without my pointing it out, an example of "x +0.100." Oops haha, o well. It isn't for a customer, and it's not nearly enough to be a sealing problem, and besides theres a big thick gasket on there already anyway. And I didn't clean off the burrs. But you can make out the tool paths pretty well. Also, the reason it isn't all one uniform z depth is honestly I was getting within low double digit thousandths of those studs.
I zeroed the z on the top face, and the bottom of the lower pocket there is -0.400. The TPS itself fit fine except for the wires sticking out, so I had to go back and add that shelf on the right. The actual length of the 3/8" 4-flute mill was 1.000 of actual flute section, and the studs were .750, and so I think that left shelf was about .300 and the right shelf I squeaked down to about .320. Reason I could get it below .250 was I had slightly more than 1.000 sticking out of the collet, plus the collet has that slight angle to it. Believe me, I took advantage of it.
It fits!

Eh, all's well that ends well.